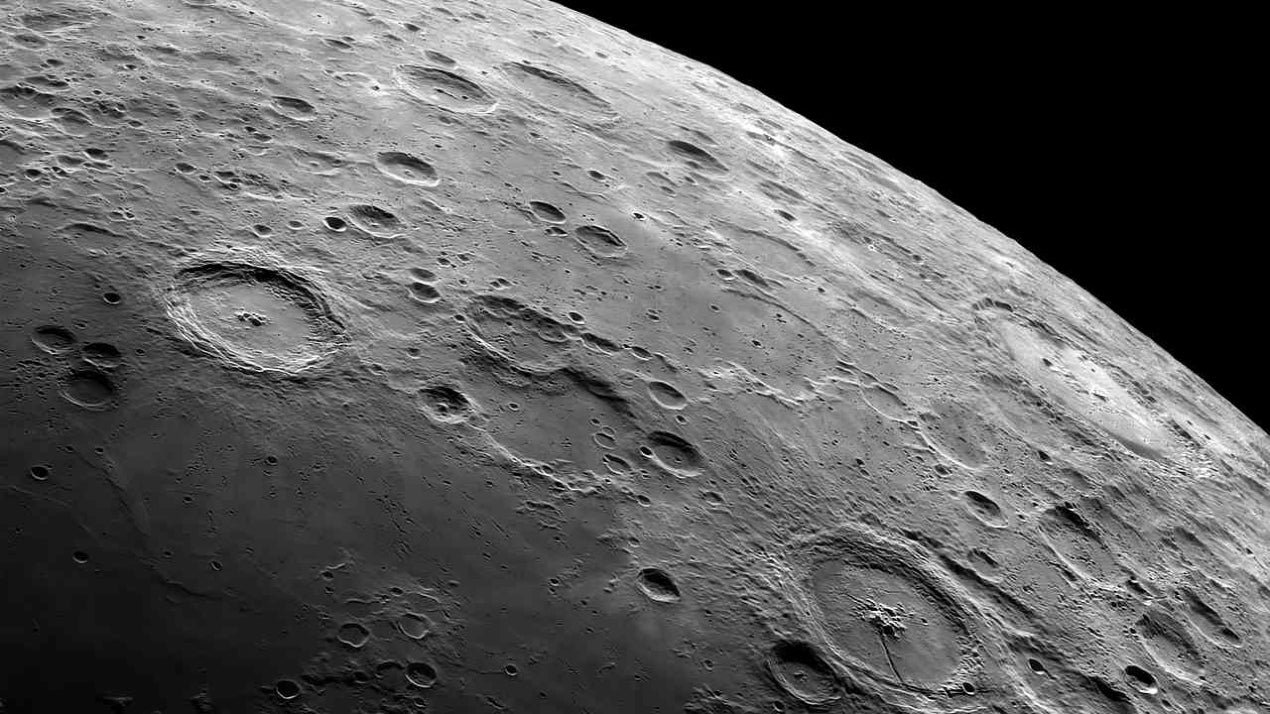
Contaminant Tolerant Scroll Vacuum Pump for Oxygen Production from Lunar Regolith
Summary
Part of my time at Air Squared was spent designing a scroll vacuum pump capable of handling vapors created in the process used to generate oxygen from lunar regolith (moon dust). In order to prevent these vapors from escaping into space and transfer them to a subsystem where they can be processed, a vacuum pump is needed. Some of the challenges included handling various harsh gases such as HF and HCl, as well as meeting flow and life requirements in such a harsh environment.
Details on the SBIR can be found here: https://sbir.nasa.gov/SBIR/abstracts/21/sbir/phase2/SBIR-21-2-Z12.01-1706.html
An article detailing the background of this project and a summary of the SBIR Phase 1 findings can be found in the LinkedIn post at the bottom of this page.
Skills Utilized:
Since I was the sole design engineer on this project, I performed every aspect of the design from conceptual design to drawing creation.
CONCEPTUAL DESIGN
Once the scrolls were sized, I created a basic, conceptual design surrounding the scrolls that incorporated allowances for isolating the working fluid and integrating a motor.
DETAILED DESIGN
Once a configuration had been settled upon, I went back over the design and reduced weight where I could while maintaining structural integrity, and I balanced the compressor with counterweights to offset the forces exerted on the housing by the orbiting scroll. I also integrated cooling allowances and made the interface with the compressor as simple as possible. I made sure the compressor was easy to assemble based on feedback from the technicians, and tried to keep machining costs down where possible by reducing the number of complex parts, expanding tolerances, and meeting with machinists to discuss ways to aid manufacturability.
BEARING CALCULATIONS
Once the design was in a good spot, I sized bearings that would be able to take the load of the orbiting scroll for the amount of hours that this vacuum pump would see usage.
FASTENER CALCULATIONS
I calculated yield/tensile strength, thread shear, and joint separation factors of safety, and in an iterative process, I calculated torques and selected a bolt size and material that would work well not only with the load that was being applied to it, but also with the thread shear limitations of the material it was being threaded into.
FEA
I performed FEA on all components that would undergo significant load. For this project, I was mostly worried about deflection at certain points in the assembly, and my analysis was used to determine where parts needed to be stiffened and where weight could be saved.
FLOW SIMULATION
I utilized Solidworks Flow Simulation to analyze the cooling channels and determine pressure drop and temperature rise across the channels.
GD&T
I created all the drawings for every component on this assembly. This consisted of heavily utilizing GD&T, as I tried to maximize tolerances where possible while maintaining functionality of the parts. Position, perpendicularity, parallelism, profile, and max material callouts all have their place on assemblies like this that require precision machined components and smooth operation.
ASSEMBLY PROCEDURE
From almost a year of working closely with the technicians on our team, I’ve learned to catch certain aspects of my design that will make their life difficult. An especially helpful way to find these errors is writing the assembly procedure that the techs will use to make the product. By creating this procedure, I am usually able to catch a few things such as wire clearances, assembly orientations, and tool allowances that would be easy to overlook otherwise.
One side of a generic scroll compressor. Two similar looking pieces interface with each other to compress the gas as it moves to the center.
Background:
What is a scroll compressor?
A scroll compressor is a simple device that consists of two main components, a fixed scroll (seen in white in the image on the right) and an orbiting scroll (seen in blue). The orbiting scroll moves in a circular motion against the fixed scroll, and as it does so, a pocket of air gets trapped between them, and is compressed as it moves to the center. Watch the red highlighted area get darker as it gets compressed.
This method of compression is advantageous for this application because it is compact, simple, requires little to no maintenance. Air Squared also specializes in oil-free scroll compressors, which don’t require lubrication to be introduced into the working fluid, which is advantageous given the potential interaction of this lubrication with contaminants in the gaspath.
A carbothermal reduction process is used to take oxides found in lunar regolith and separate them into their respective components. The first step in this process is melting the regolith. This is done in the presence of carbon and methane, which react with the metal oxides to create CO and H2, among other trace gases. These gases are then collected by the vacuum pump and sent to the next step in the process. These are then converted to CH4 and H2O, and the water undergoes hydrolysis to convert it into H2 and O2.
One of the challenges of designing this pump was that the vapors produced by melting the regolith have many impurities (hence the contaminant tolerant portion of the title). The vacuum pump will have to withstand both high levels of dust and trace acid vapors, such as HCl, HF, and H2S. For this reason, it was important to use proper materials that would be able to withstand these substances without degradation or stress corrosion cracking. It was also important to isolate this working fluid from both the sensitive internals of the vacuum pump housing (motor, bearings, etc.) and and any surrounding components in the system.
The Vacuum Pump’s Role in the Generation of Oxygen on the Moon
A general system layout of a carbothermal reduction process, note the position of the vacuum pump in the system.